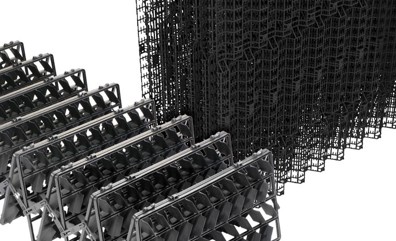
Cooling tower packings or fillings are actually a set of intermediate surfaces and volumes that can increase the air contact level in the cooling tower. This increase in level will eventually increase the rate of evaporation and thus increase the efficiency of the cooling tower.
Some consider the mechanism of the heart and core’s cooling towers to be water, while the purpose of the cooling tower is to reduce the temperature of the water in the industrial line, and if we look more closely, the heart of a cooling tower is its packings.
Types of packing
In general, two basic types of fillings can be enumerated: Film packings and Splash packings. Splash packages, as their name implies, increase the air contact surface by spraying and creating a kind of disturbance in the water spray. Film packings, on the other hand, are a medium for the formation of film surfaces on their surfaces. It can be said that in film packings, heat exchange takes place between the surface of the water film formed on the surfaces and air, and in splash packing, heat exchange takes place between the surface of the air droplets in the space between the packings.
Flute
The pattern of placement of surfaces in packings can be diagonal or straight, these channels are called flutes. Flutes are designed to move water as far as there is potential to move water. Smaller flutes are usually more cost-effective because they will have more capacity in a fixed volume. Larger flutes in packings, on the other hand, can be used for applications where there is dirty water because they are less clogged than packings with smaller flutes. Larger flat packing, while sacrificing high productivity and efficiency, will allow dirtier water to move between surfaces.
Types of risks in packing
Although fillings play a key role in the cooling tower, there are many risks to the efficiency of these components. Due to the special application of the cooling tower and also choosing the right type of packings in the design of the cooling tower, it is possible to reduce the efficiency of these parts. Among the risks in packing, the following three categories can be mentioned:
Sedimentation risk
Scaling Risk, which depends on the hardness of the water and the amount of sediment in the working fluid. By choosing the right type of anti-fouling packages, this risk can be prevented from increasing. It should be noted that splash packings are generally less prone to fouling due to their lower contact surfaces with water flow. For this reason, this type of packing is also called anti-fouling packing.
Risk taking
Due to the presence of microorganisms in the water and the fact that the cooling tower is always involved in climate transactions due to its type of mechanism, Fouling Risk should be considered a serious risk for some industries. With the growth of microorganisms and not choosing the right type of packing, industrial lines can suffer great losses. By choosing packages with anti-microbial substances and choosing the appropriate type of packing for the industrial line, the risk and risk of clogging can be greatly reduced.
Risk Legionella
Legionella is one of the most dangerous bacteria that grows in sunny environments where water stays for a long time. Legionella bacteria can cause many problems, including respiratory problems. The use of packings that increase the likelihood of bacterial growth can also increase the risk of bacterial growth and proliferation. As mentioned, anti-microorganism packages as well as packages that have a lower contact level can reduce this level of risk.
Factors influencing the choice of packing
According to the above, many factors should be considered in the selection of packings, including important factors in the selection of packing can be considered the amount of environmental pollution and the type of environmental pollution. Water quality is another basic parameter in choosing the type of packing. Among the microfactors affecting water quality and its effect on the choice of packing, we can mention the type of water (sea, river, well, dam, etc.).
The type of industry in which the cooling tower and consequently packing is used is also influential in choosing the type of packing. For example, whether packings are used in the chemical industry or in industry can have a great impact on the choice of packing. By identifying other issues related to water quality such as water cycle type and values related to water quality and water treatment type, the coefficients related to three risk items can be examined and the type of packing with the best thermal efficiency and functional efficiency and the lowest risk in terms of health And chose an operation.
Packing material
Packing material can be many materials. The first materials used to make packings were wood, especially red wood. Most of the old cooling towers used splash bars that placed the wooden boards inside the cooling towers with precise and calculated arrangements.
Although these types of packings were used in the past, they did not have the efficiency of today’s designed packings. Other materials used to make packings include ceramics or metals. With the widespread use of plastic materials such as PP, PVC, PE, ABS and the expansion of the production of these materials, the packings and fillings that are produced today all use plastic materials.
The use of plastic materials does not have all the disadvantages of other packings, such as wood packings, which increase the risk of microorganisms growing, or metal packings, which have the potential for corrosion. But among the various plastic materials, the use of some of the packages produced can have more added value. Many plastics are less durable than other plastics, as well as less resistant to heat, and can also be very harmful to the environment due to their irreversibility to nature.
PP and PVC packings
Among all the materials used for the production of packings and fillings, and especially for cooling towers, more emphasis is placed on packings with materials such as PVC and PP. Polypropylene is one of the most widely used plastics in the world, which in addition to all its unique advantages among other plastics, has the ability to return to nature. It is a non-toxic and odorless substance that weighs very little and has good hardness and toughness at the same time. In addition to its good physical properties, it has a high chemical resistance to chemical solvents, bases and acids. This polymer has less weight and more flexibility than other polymers. The most common use of polypropylene is in injection molds, in which PP packings are usually produced. One of the most important factors that distinguishes PP packing from PVC packing is that the sheets and packing surfaces in PP packing can be welded together by heat welding, while in PVC sheets, special packing sheets must be bonded by adhesive. Will happen. In maintenance, as well as in industries with applications where the water temperature is high, these connections made by the adhesive have a high probability of detachment of the packing sheets. In adhesive-bonded sheets, it is possible for the sheets to separate without an external agent over time, while in PP packings that use thermal welds, this is not possible.
There are many characteristics in comparison of PVC and PP that can make different industries more determined in deciding to buy PP packages, for example higher temperature resistance PP or 15 to 20 years life of PP packages as well as deposition rate of packings with these materials due to lower surface adhesion . Due to the low surface roughness of these packings, ie PP packing, less pressure drop will occur in the cooling towers, which will have a significant effect on the efficiency of the cooling tower. As mentioned, the high chemical resistance of polypropylene makes the PP packing high resistance to acid washing and washing. PP packings are also highly resistant to additives such as chlorine, which are used to prevent biological fouling in water.